RESTORATION (4)
Body Panels and Seats
As I do pieces and parts up for the GPW, I'll be adding photos
to this section.
REAR SEAT
After
drawing up the different sheeting on the rear seat I thought it was about
time I put them into practice, and find out if what I had drawn was
usable. After talking to my panel bloke Shane Sommerfeld at Summy's Smash
Repairs ( same bloke that did all
the work on my Cj3B) I found that the reio ribs are best put in
first, and it requires that the ends are left square and not cut out to
shape. Also due to the process of putting in the ribs, the metal will
distort slightly. So having that
information in hand, I picked up a suitable piece of 18g,
cut with a workable area all around and marked a centre line from which I
then marked the length, and position of the ribs. Next was the fun bit,
Summy didn't have the correct shape the original seat pan had pressed into
it, so using a profile gauge he made a male and female tool to fit his
machine. This isn't the roller type commonly used to roll in the shape,
but a reciprocal action type, which only requires small 3/4" block dies. A
photo of the machine and a test piece for the seat is on the
left.
Having
checked that the depth, width, and profile were correct against the
original, it only took about 20
minutes to press in the
ribs. We do all of Summy's screenprinting, so he can expect some discount
on the next job too. That's Summy on the right, (left pic) with one of his
employees just about to remove the piece after the last rib was finished.
After the pressing was completed the ends were tapped and shrunk, leaving
the pan ready to be marked out. (right pic)
I took
the piece home, marked out the finished size, took it up to another mates
place, Steve Walker,
who has a large plumbing business used his guillotine
and folder, again at no cost to me.Within an hour I had the ends trimmed
and shaped, the small side ends were folded up, I then attached the pan to
the frame with a vise and G clamps, using a panel hammer and a block of
wood, rolled the edges to the frame shape. All that remains then is to
attach it to the frame.
SEAT FRAME
The Frame was in excellent condition with
only slight rust pitting when I removed the old seat pan. I first bead
blasted where all the spot welds apparent, so I could drill them out. I
also took many pics where the old spots were located so I could duplicate
them as near as possible with the new pan. I attached the pan back onto
the frame, made some adjustments in accordance with the drawing, clamped
it down, drilled using a spot drill, and brazed the pan to the frame.
Caution....if you do it this way be aware of heat and what it can do to
sheeting, so knowing that, alternate the "spots" and use a sponge to cool
down things after each weld. Things went smoothly, with no buckling, or
movement.( Whew!. that was a relief! and called for a cold one)
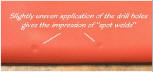
Having
removed the old pump bracket, I made up a stud and pressed in the
recess, (Pic on the lower left) then purchased some 1' x 1/16" wall tubing
( this is extremely cheap, a length 88inches - 2.25m, cut to size was only
AU$6 - US$3, I got extra for the repairs to the top bows which I'll
probably do next. I marked out the centre line of the tubing and drilled
1/4" holes at the intervals from the original, I just laid up the old tube
against the pan and marked the sheeting, so easy. The tubing was
clamped into place and I welded the tubing through the holes. After
each weld I again used the sponge to cool things off. If you clamp as near
as possible to the weld, ( and I used an arc welded for this not brazed) ,
you won't get any buckling, A Mig Welder would have worked even
better.
 
The old pump bracket was sand blasted, again
I drilled through the sheeting and welded directly to the back side of the
bracket. This allows the old spot welds from the original to be seen, (Pic
on the right) and it makes it look the same as the original.
The excess weld material was ground of, and
sandblasted again and primed.
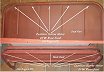
When I get this correctly painted I'll
consider this part completed, but it's been fun to do.
Home Restoration
1
2
3 g503.com
|